Fieldwork Lessons Learned Part One: Tech Development and Project Management
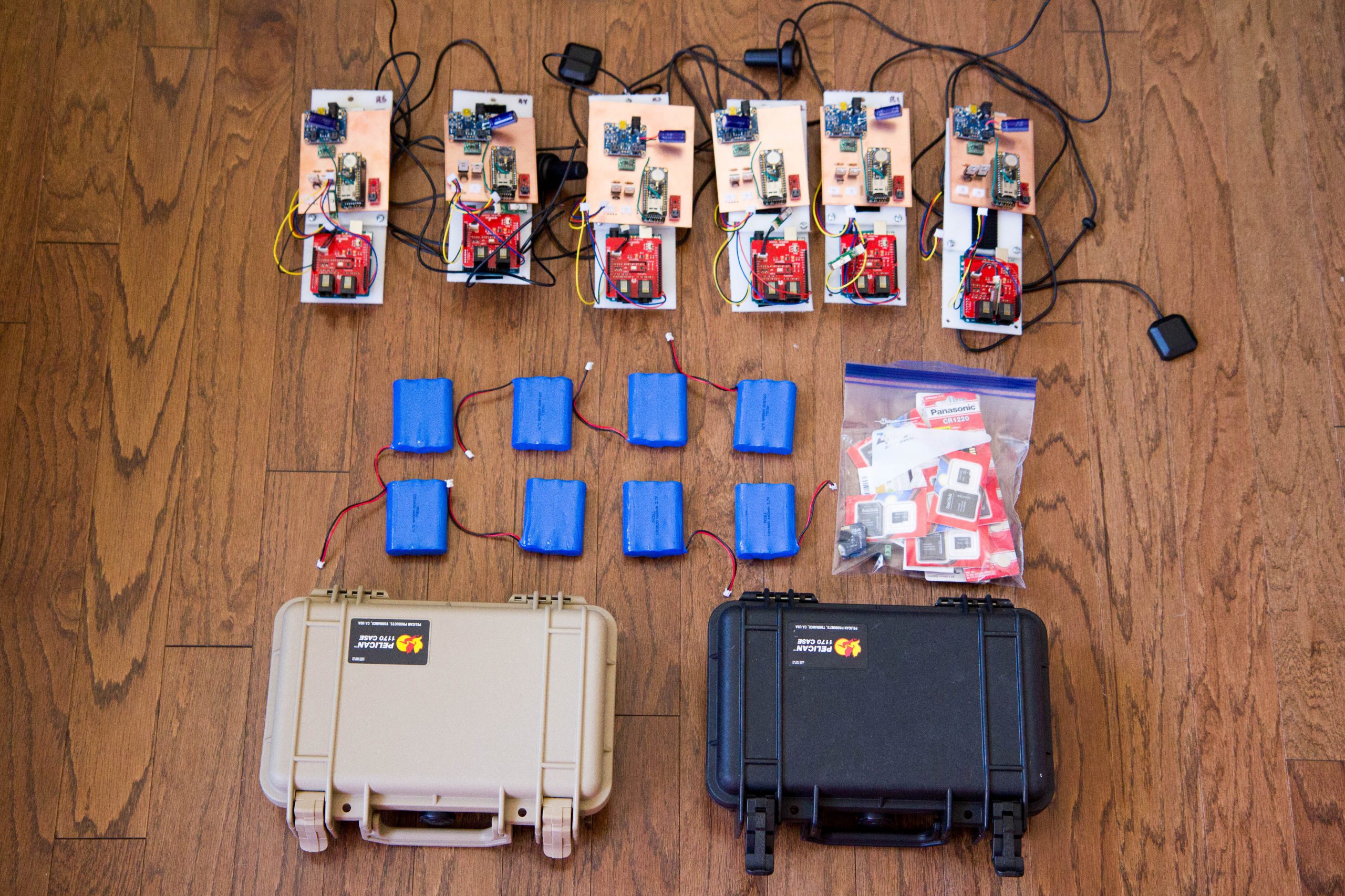
Our team has experienced all kinds of things in the course of deploying conservation technology in the field. What have we learned? A lot. We recently had a discussion internally that ended up moving to Twitter, where we got even more great ideas from our friends and followers. So many, in fact, that we had to break it up into multiple blog posts.
These tips will cover what you need to think about long before you actually make it into the field, while you’re developing the technology and putting together a project plan. Stay tuned for future posts covering recommended tools, packing and travel, and actually getting into the field.
Tech Development
- Test early and test often. You want to fail early and fail fast.
- Scope creep is a real issue. Do the work upfront to capture the requirements and build to that. Any additional work can happen on later iterations.
- Project management is absolutely critical. If you can afford to bring on someone who is skilled at that, it can help to increase the probability of success a lot. Try to give the job to someone not involved in technology development directly.
- There is a very long distance between the maker space and a field site.
- Fully integrate the system in the lab, and in a local field test, before deploying.
- Never deploy anything without a proper, functioning watchdog timer. (credit to @ChrisLDutton)
- If you need a RTC (real-time-clock) or GPS, make sure you add it.
- Never deploy in the field without a test deployment of at least half as long as your true deployment, and in similar conditions (humidity, heat, etc). Testing in similar conditions is a huge thing. (credit to @ChrisLDutton)
- Maintenance and end-of-life of the tech is a critical part of any solution (in both technical and cost aspects), especially with respect to locally-available repair and replacement.
- Community participation needs to be baked in from the very start.
- Usability is an important driver of success. Make sure to design the tools to work appropriately for the folks who are using it.
- Make sure that the data your technology is collecting actually solves the problems your project partners are looking to solve.
- Connectivity is likely going to be bad in the area that you are deploying your tech, so plan accordingly with respect to data collection, troubleshooting, and other issues.
- It generally helps to pick enclosures with an IP rating greater than what you need, but they lose their ratings once you drill holes or cut into them without taking appropriate measures.
- Don’t overcomplicate things; choose simple or COTS solutions in places where it is easiest. Sometimes it is easiest to repurpose an existing tech.
- Try to never design a solution without visiting the site first. What works in one place won’t necessarily work in another.
- Pick the right battery for your environmental conditions. Size it with CONSIDERABLE margin.
- Gaskets and plastics can degrade over time from UV/temp so choose your materials carefully and deploy accordingly.
- Think outside the box and bring your imagination to deployments. No matter how prepared you are, you will be surprised.
- If using radio transmitters, double check the frequency & signal strength before deployment. And don’t count on that battery lasting until it’s estimated end date. (credit to @SarahECarter2)
- Plan for losses, and how you will handle them. (credit to @sarameghanbeery)
Project Management
- Traditional NGOs like funding field costs, equipment costs, and lab costs. Salaries are harder to get funded, but try foundations or research organizations and government agencies.
- Create a schedule and test plan, identify risks early and work on them ASAP, and have a regular meeting/reporting structure.
- Think about maintenance early. Who does it? How much does it cost? Are parts available?
- Form partnerships early. Engage with the community where this tech will be deployed and understand the constraints that come from working there.
- Be honest about technological capabilities and the skills of team members. Use this to manage expectations. Be realistic, do not promise the world!
- Order the parts and field supplies as early as possible. Shipping will always take some time and you’ll need room for last minute purchases. If you can identify brick-and-mortar locations for supplies, that can be a lifesaver.
Do you have additional tips to add to the list? Share them with us @FieldKitOrg on Twitter and we’ll include them in our lessons learned!